Practical EHS Tips, News & Advice. Updated Daily.
You must provide your employees with personal protective equipment (PPE) when other methods higher in industrial hygiene’s “hierarchy of controls” like elimination, substitution, engineering controls, and administrative controls are not enough to protect their health and safety. Carbon fiber face mask
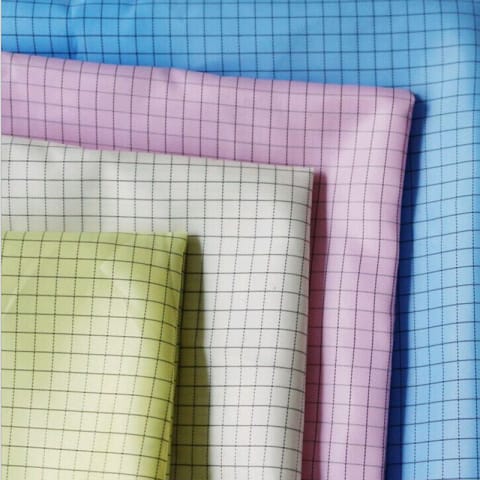
PPE protects workers’ eyes, faces, feet, hands, and heads, and protective clothing may protect the entire body from chemical or electrical hazards. Respirators protect workers from dust, gases, particles, and infectious diseases, and you can protect workers at your facility from falls from heights with personal fall arrest systems.
Many Occupational Safety and Health Administration (OSHA) standards require that employers provide protective equipment, including chemical protective clothing or equipment, face shields, fall protection equipment, gloves, goggles, hard hats, safety glasses, safety shoes or boots, and welding goggles and helmets.
OSHA’s enforcement guidance for PPE (CPL 02-01-050) outlines the agency’s interpretations of the general industry PPE standards (29 Code of Federal Regulations (CFR) Part 1910, Subpart I) and its procedures for enforcing them. The enforcement guidance clarifies what type of PPE employees must be provided at no cost, when employers must pay for PPE or replacement PPE, and when employers are not required to pay for PPE.
There are a few exceptions to OSHA’s requirement for employer payment for PPE—back belts, everyday clothing, nonspecialty footwear worn off the jobsite, ordinary cold weather or rain gear, and ordinary prescription eyewear.
Under OSHA regulations, you must pay for PPE required by OSHA standards. During an inspection, agency compliance safety and health officers (CSHOs) will determine employee-employer relationships at a facility or worksite, establishing who must pay for workers’ PPE.
OSHA’s general requirements for PPE include assessing workplace hazards and selecting appropriate equipment, employer payment for PPE, training, and preventing the use of damaged or defective PPE.
You also must assess hazards that are present or likely to be present in the workplace. OSHA regulations require a written assessment verifying the hazard assessment, identifying the person performing the assessment, and the assessment date. Additionally, you must select appropriate PPE and communicate your selection decisions to your employees.
During an inspection, agency CSHOs will determine whether you have assessed all workplace hazards and selected appropriate PPE.
Your PPE training must cover:
You also need to ensure your employees understand their training and retrain if necessary, such as when there are changes in workplace conditions or the types of PPE used. An agency CSHO will assess the effectiveness of the training you provide during an inspection.
According to OSHA, thousands of workers are blinded each year from work-related eye injuries. Eye injuries can result from small objects or particles such as cement chips, dust, metal slivers, and wood chips scraping or striking the eye and chemical or thermal burns, and eye hazards include arc welding, chemicals, lasers, objects, and particles.
Proper selection and use of eye and face protection can prevent occupational eye injuries.
OSHA’s construction industry eye and face protection standard (29 CFR §1926.102) is the agency’s ninth most frequently cited standard. The agency cited 1,401 violations in fiscal year (FY) 2022. OSHA also has general industry (§1910.133), shipyard (§1915.153), and longshoring (§1918.101) standards for eye and face protection.
Eye protection must be maintained in good condition. If eye protection is reused, you must clean and disinfect it before issuing it for another employee’s use. If an employee wears prescription eyeglasses, the eye protection you provide must be a type that can be worn over glasses.
OSHA’s respiratory protection standard (§1910.134) is the agency’s third most frequently cited standard, cited 2,185 times in FY 2022. It requires a written respiratory protection program, medical evaluation for respirator use, initial and annual fit testing, respirator cleaning and disinfection, recordkeeping, and training.
Types of respirators include filtering facepiece respirators like N95s or P100s, elastomeric half-mask respirators, elastomeric full facepiece respirators, powered air-purifying respirators, supplied-air respirators, self-contained breathing apparatuses, and combination supplied-air/self-contained apparatuses.
An OSHA inspection for respiratory protection compliance will check whether your program addresses all the standard’s requirements, including respirator selection; equipment cleaning, maintenance, and repair; fit testing; and training.
Head protection includes hard hats or helmets to protect your employees from falling objects and helmets designed to reduce electrical shock for those working near exposed electrical conductors that could come into contact with the head.
Hard hats or helmets must meet the requirements of one of three industry standards: American National Standards Institute (ANSI) Z89.1-2009, “American National Standard for Industrial Head Protection”; ANSI Z89.1-2003, “American National Standard for Industrial Head Protection”; or ANSI Z89.1-1997, “American National Standard for Personnel Protection—Protective Headwear for Industrial Workers.”
ANSI Z89.1-1997 includes specifications for the electrical performance of Class G and Class E electrical helmets.
During an OSHA inspection, agency CSHOs will look for protective helmets that resist penetration by objects, absorb the shock of a blow, are water-resistant, and have slow-burning properties. They also will check that you are following the manufacturers’ instructions for proper adjustment and replacement of the helmet suspension and headband.
Wherever there is a danger of foot injuries from falling or rolling objects or objects piercing the sole, you must ensure your employees have and use protective footwear.
Footwear must meet the specifications of one of the following industry consensus standards:
During an OSHA inspection, a CSHO will first confirm that you have completed an assessment of foot injury hazards. If foot injury hazards are present in your facility, the CSHO will confirm that workers have footwear that meet the requirements of one of the industry consensus standards.
The CSHO may also check for the following:
Hazards requiring hand protection include skin absorption of harmful substances; chemical burns; harmful temperature extremes; punctures; severe abrasions, cuts, or lacerations; sharp objects; and thermal burns.
Moreover, you must provide employees with hand protection appropriate for the working conditions and hazards identified in your facility. An agency CSHO will check during an inspection that all affected workers have appropriate hand protection whenever hazards cannot be eliminated through engineering, work practice, or administrative controls.
You must provide hearing protection whenever workplace or worksite noise levels exceed permissible noise exposure levels (PELs) and feasible administrative or engineering controls cannot reduce the noise level to below the PEL. You can find a table of permissible noise exposures in §1910.95(b)(2).
Moreover, you must have an ongoing hearing conservation program that includes exposure monitoring; baseline and annual worker audiogram testing; hearing protectors, such as single-use earplugs, preformed or molded earplugs, and earmuffs; and training and recordkeeping programs.
Agency CSHOs will assess noise exposures and the effectiveness of all elements of your hearing conservation program and hearing protector use.
Electrical protective equipment includes rubber insulating blankets, rubber insulating covers, rubber insulating gloves, rubber insulating line hoses, rubber insulating matting, and rubber insulating sleeves.
During an OSHA inspection, the CSHO will check for the following:
OSHA’s construction industry fall protection standard is the agency’s most frequently cited standard. In FY 2022, OSHA cited 5,260 fall protection violations—more than double the number of violations (2,424) of its second most frequently cited standard (hazard communication).
Fatalities caused by falls from elevation remain a leading cause of death for construction workers, according to the Bureau of Labor Statistics (BLS). Falls from height are one of the construction industry’s “Fatal Four” safety hazards, along with caught-in or -between, electrocution, and struck-by hazards.
The construction fall protection standard requires guardrails, safety nets, or personal fall arrest systems. Safety net systems can be installed underneath trusses to prevent workers from falling to a lower level but also must prevent worker contact with a surface or structure in the event of a fall.
A personal fall arrest system consists of three components:
Workers also must be trained in the nature and hazards of falls and the use and limitations of fall protection equipment.
OSHA’s general industry fall protection also requires personal fall arrest systems composed of an anchor, a harness, and a lifeline to protect workers from falls from height. The general industry standard also contains fall protection requirements for linemen and window cleaners.
If an OSHA inspector identifies workplace hazards not adequately controlled by administrative and engineering controls or work practices, the inspector will check that employees have been provided PPE.
Inspection guidelines include checking that:
Your email address will not be published. Required fields are marked *
Save my name, email, and website in this browser for the next time I comment.
This site uses Akismet to reduce spam. Learn how your comment data is processed.
LATHAM, NY – September 12, 2023 – Protective Industrial Products, Inc. (PIP®), a global leader in personal protective equipment (PPE) including hand protection, above-the-neck protection, workwear and footwear, proudly announces the launch of THORZT™ into the North America market. This exciting new addition of powder concentrates enhances the PIP® market-leading heat stress PPE portfolio. THORZT™ […]
Judges note Avetta’s “impressive” platform helps companies improve ESG performance across the entire supply chain August 31, 2023, LEHI, Utah & HOUSTON—Avetta® has been awarded a Gold Stevie® Award in the Supply Chain Management Solution category in the American Business Awards® and a Silver Stevie® Award in the Compliance Solution category in the International Business […]
OSHA violations are rampant, hide in plain sight, and have potentially dire consequences for your people and your bottom line. Every year, thousands of preventable incidents occur, causing needless injuries, illnesses, and in some cases – deaths. From OSHA penalties to workers’ compensation claims to legal, operational, and reputational costs, businesses can pay a significant […]
B2B veteran brings deep experience in high-growth business and scaling with a human-centric and forward-thinking approach LONDON, UNITED KINGDOM – August 21, 2023 – EcoOnline, a leading EHS and ESG global software provider, is pleased to announce the appointment of Tom Goodmanson as its Chief Executive Officer. As a proven CEO that has built global, industry-leading high-growth […]
Next-generation IoT system digitizes daily processes, adds capabilities, streamlines logistics and provides actionable, on-demand machine insights. McConnellsburg, PA (August 17, 2023) — JLG Industries, Inc., an Oshkosh company [NYSE:OSK] and a leading global manufacturer of mobile elevating work platforms (MEWPs) and telehandlers, now offers standard ClearSky Smart Fleet™ connectively on most new JLG® equipment. This breakthrough IoT (Internet […]
OSHA violations are rampant, hide in plain sight, and have potentially dire consequences for your people and your bottom line. Every year, thousands of preventable incidents occur, causing needless injuries, illnesses, and in some cases – deaths. From OSHA penalties to workers’ compensation claims to legal, operational, and reputational costs, businesses can pay a significant […]
Is it possible for organizations to check all the right boxes and still not have the efficiency and safety culture that they desire? Safety culture needs to be entwined throughout an organization. We recently surveyed over 200 EHS Professionals to see how their organizations tackle safety initiatives. 75% feel they are NOT very effective in preventing […]
In our recent global research, more than 75% of respondents reported they expect to lose customers and skilled workers if they don’t improve their ESG and EHS performance. More than 50% struggle to collect the data they need for effective, proactive ESG and EHS programs, while fewer than 50% are confident in the quality of […]
What are the unexpected costs manufacturers face amidst the workforce shortage? Learn about industry challenges and a leading tech solution in this infographic! Download today!
Sponsored by: Superior Glove Not surprisingly, injuries caused by knocks, bumps, and pinches are among the most common across various industries and can cause a wide range of hand injuries. When an object strikes or pinches a hand, the force is transferred directly from the object to the hand and can lead to injury. This is known as an impact injury. From minor bruising to broken bones, fractures, or contusions, workers need to keep their hands safe by using the right protection for the job. Learn more!
Disposable Sticky Product The mission of EHS On Tap is to provide clear, relevant, actionable information on topics that matter to EHS professionals in podcast form through engaging and insightful interviews with experts and thought leaders. Listen to the latest and subscribe!